

Unless you have a bushing driver of the correct size pounding them in will not work. You could heat the end bells with any torch or a bearing induction heater and maybe even with an electric frying pan, and simply drop the sleeve bearing in place. Normally a hydraulic press or an arbor press is used. Either a slit or a groove, thinning the wall in one area or two opposite areas.Īfter you have them removed, clean up the housing and remove and burrs. You don't have to cut all of the sleeve bearing out. If you have a die grinder or dremel, you can cut them out, just be careful not to damage the end bell. So far my guess is none of these are on your radar They could be machined out on a lathe or vertical milling machine. I don't know about MAPP gas, but a Propane torch likely will not produce enough heat fast enough. If you don't have an ox-acetylene torch or access to one you could use a morgan-knocker / slide-hammer style puller with the right attachment. That is your warning to stop heating the end bells. The soot will burn off about 100 degrees lower than the melting point of the aluminun. You could use multiple ways to measure that, a 600, 650, or 700 degree welders temp stick, an infrared thermometer, or adjust your flame to a carbonizing flame, one with inadequate oxygen / excess acetylene / one that makes black smoke. If you do, scrap the motor.Īluminum will melt somewhere around 765 degrees F, depending on its composition. torch and if you have aluminum end bells be care not to melt them. The end bells expand from the heat and the sleeves should fall out. The fast easy way - set the end bells on 2 blocks or stand-off spaces and heat the bearing housing area with an ox-acetylene torch with a rose-bud tip or a larger welding tip. Depending on your skills and tool you have this could be a task. Next remove the sleeve bearings from their seat. If you don't have a dead-blow, use a a 2-3 hammer or whatever you have with a hardwood block protecting the shaft so you don't mushroom the shaft end.Īfter you remove the ODE end bell from the shaft, you can repeat the proceed and rap that end of the shaft to pop the DE end bell out of the frame.or take the rotor out and use a block of wood thru the stator. I would use a rubber-faced dead blow hammer and rap the end of the shaft. If they are worn badly or sized to the shaft, the task could be more difficult. With sleeve bearings, if they are in good condition, it should be easy. Remove the screws that hold the end bells to the frame. You can use a permanent marker or scribe for that. It may help with re-assembly, eliminating rotating the end bells in attempt to get the thru-bolts into holes you can't see inside the motor. If you have a rolled steel frame (basically a tin-can) with thru bolts, it would be a good practice to index the end bells to the frame, meaning put some line-up marks across the split between the frame and end bells. That was for cast iron frame motors with bolts thru the end bells into the frame.
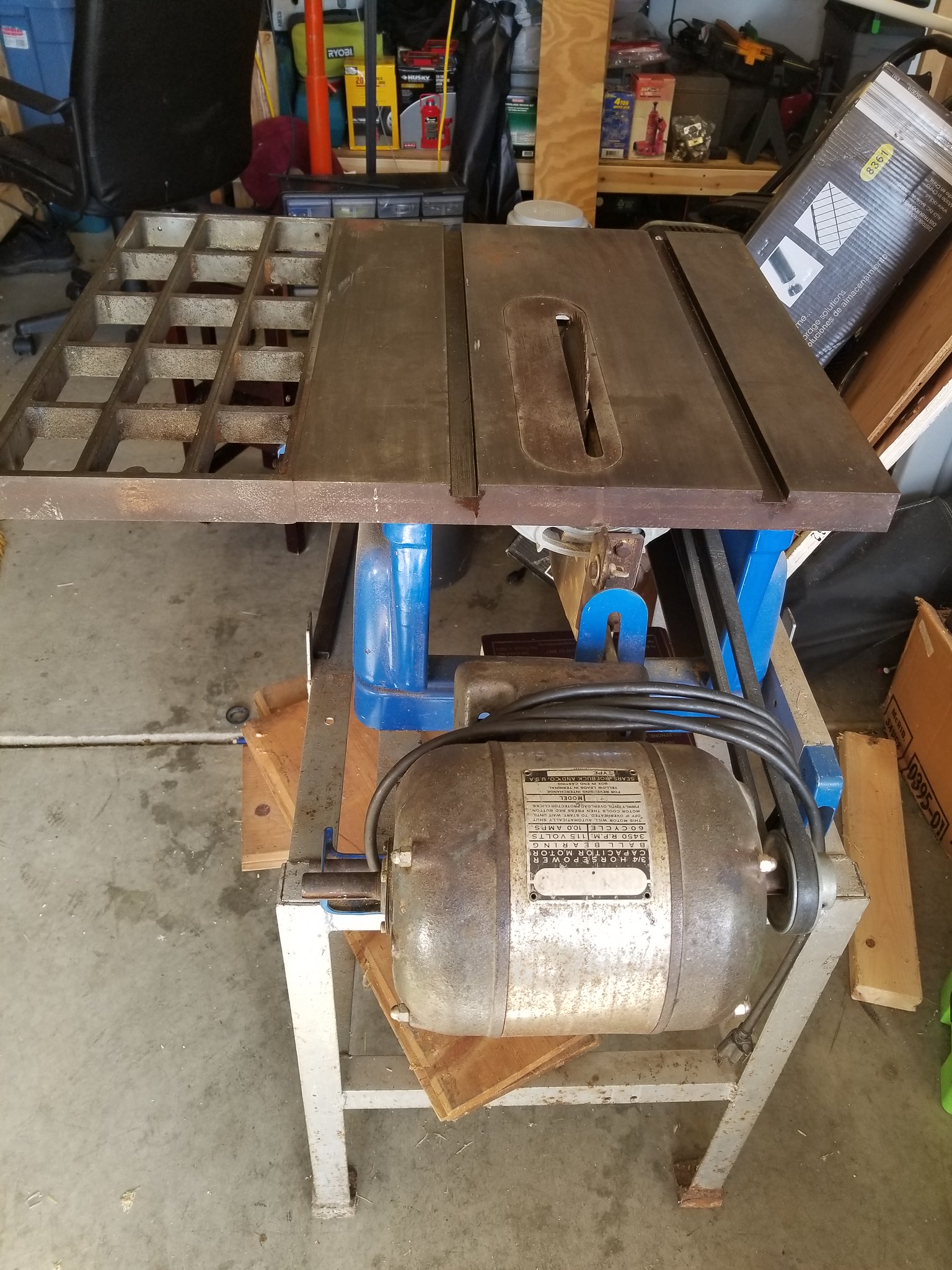
Opposite Drive End / Fan End if so equiped We always punched them with a center punch on the top of the motor:ġ mark for O.D.E. Mark the end bells to ensure not mixing them up later and to aid in reassembly. If the motor is TEFC - Totally Enclosed Fan Cooled remove the fan schrod and fan Remove the pulley if it is a belt drive / drive coupler etc. On a single phase, 110v that should not be a problem, but an ounce of prevention will prevent any problems In the process, if you remove any wires, and they are not color coded or labeled label them. Thank youI would try Sears first or their parts direct website for the bearing or a motor If not extension tubes will be added to make the caps easily accessible. I'm afraid the cost of a motor shop will be about the same.Ĭan the sleeve bearing be replaced with ones that don't need to be oiled? The saw gets loaned out on occasion. Harbor freight wants more for a motor than I paid for the saw. Can someone point me to instructions on replacing the sleeve bearings on this 1 hp table saw motor? I believe it was made in the 80s.
